Poziom drgań zespołów pompowych – racjonalne wymagania
1. Wprowadzenie
Poziom drgań zespołów pompowych jest istotnym parametrem mającym znaczenie dla prognozowania ich żywotności. Stanowi ponadto ważne kryterium oceny jakości wykonania pompy. Między innymi z powyższych względów poziom drgań powinien być brany pod uwagę jako jeden z czynników wpływających na wybór zespołu pompowego. Jeśli zakup zespołu pompowego odbywa się na podstawie specyfikacji wymagań technicznych, w dokumencie tym dopuszczalny poziom drgań powinien zostać określony. To czy taka sytuacja ma miejsce zależy w znacznym stopniu od branży, do której zespół pompowy jest przeznaczony i od obowiązujących tam standardów technicznych. Można stwierdzić, że znaczny wpływ odgrywają w tym zakresie przyzwyczajenia i tradycje. W niektórych gałęziach przemysłu na kwestię poziomu drgań nie zwraca się niemal uwagi. Przeciwna sytuacja ma miejsce np. w energetyce i petrochemii, gdzie do drgań przykłada się znaczną wagę. W większości specyfikacji wymagań technicznych dotyczących pomp energetycznych określone są wymagania dotyczące poziomu drgań co należy ocenić pozytywnie. Zdarzają się jednak sytuacje, gdy zamawiający arbitralnie narzuca zbyt wygórowane wymagania.
Niniejszy tekst poświęcony jest omówieniu wymagań dotyczących drgań jakie powinny być formułowane na etapie wyboru i zakupu zespołów pompowych.
2. Parametry służące do oceny drgań zespołów pompowych.
Można dokonywać pomiarów różnych parametrów dotyczących drgań lecz jako podstawę oceny stanu dynamicznego maszyny powszechnie przyjmuje się średniokwadratową wartość prędkości drgań wyrażoną w mm/s. Jest to wielkość fizyczna związana z energią kinetyczną drgań. Zgodnie z normą PN-ISO 10816-1 pomiaru dokonuje się w typowym przypadku na niewirujących obudowach łożysk, w dwu kierunkach wzajemnie prostopadłych i prostopadłych do wału.
Prędkość drgań jest w zdecydowanej większości przypadków wystarczającym kryterium oceny dynamicznej zespołu pompowego na etapie wyboru i prób odbiorczych.
Inne parametry takie jak m.in.: przemieszczenie drgań, przyspieszenie drgań, drgania względne wałów wobec elementów niewirujących, analiza widmowa stanowią cenne narzędzie diagnostyczne lecz ich uwzględnianie w ramach prób odbiorczych wydaje się zbędne poza szczególnymi przypadkami, gdyż zwiększa koszt badań.
3. Drgania jako zjawisko fizyczne
Drgania pomp z punktu widzenia fizyki są mechanizmem przekształcania energii od silnika napędowego w energię kinetyczną ruchu oscylacyjnego elementów pompy, która następnie jest rozpraszana w postaci ciepła na skutek wewnętrznego tłumienia w materiale. W pompie jest to zjawisko uboczne, niezamierzone i niekorzystne, gdyż energia od napędu powinna być przekazywana do cieczy. W niniejszym tekście nie ma miejsca na szerokie opisywanie teorii drgań, która ma szeroką literaturę np. [1, 2]. Celem uzasadnienia wniosków jakie z niniejszego artykułu mają wynikać wspomnimy w tym miejscu jedynie, że poziom drgań zależy od intensywności wymuszeń, czyli mechanizmów na skutek których energia drgań jest przekazywana oraz od sztywności, częstości drgań własnych oraz zdolności tłumienia konstrukcji pompy i jej posadowienia.
Czynniki wymuszające drgania można podzielić na dwie podstawowe grupy. Pierwsza z nich to wymuszenia o charakterze mechanicznym. Zaliczyć tu można czynniki takie jak niewyważenie zespołu wirującego, niewspółosiowość pompy i silnika, oddziaływanie łopatek wirnika z językiem spirali lub łopatkami kierownicy. Nad czynnikami z tej grupy pełną kontrolę ma producent zespołu pompowego, do którego obowiązków należy takie zaprojektowanie i wykonanie pompy aby wymuszenia te były na odpowiednio niskim poziomie intensywności. Należy zaznaczyć, że pełna eliminacja wymuszeń o tym charakterze nie jest możliwa, gdyż dla przykładu nie da się całkowicie uniknąć wpływu siły odśrodkowej działającej na zespół wirujący, gdyż nawet przy idealnym wyważeniu pewna siła odśrodkowa wystąpi na skutek ugięcia wału, który nigdy nie posiada nieskończenie wielkiej sztywności. Podobnie, przy zastosowaniu wirników o skończonej ilości łopatek nie da się w pełni wyeliminować ich oddziaływania z elementami niewirującymi.
Druga grupa to wymuszenia o charakterze hydraulicznym. Zaliczają się tu drgania generowane przez kawitację oraz na skutek pracy pompy z dala od optymalnej wydajności. W tym drugim przypadku w układzie przepływowym powstają wiry (przepływy recyrkulacyjne) absorbujące energię od napędu i przekazujące ją na generację drgań. O ile w przypadku drgań wymuszanych mechanicznie ich częstotliwość jest określona (najczęściej obrotowa lub łopatkowa) to w przypadku wymuszeń hydraulicznych drgania mają charakter szumu bez wyraźnie dominującej częstotliwości. Drgania generowane przez przepływy recyrkulacyjne z reguły występują w paśmie częstotliwości wyraźnie niższej od obrotowej. Uniknięcie przepływów recyrkulacyjnych i spowodowanych przez nie wymuszeń hydraulicznych jest praktycznie niemożliwe przy pracy z dala od parametrów nominalnych. Z tego powodu od producenta (projektanta) pompy można wymagać dotrzymania określonego poziomu drgań w zakresie wydajności w pobliżu nominalnej. Natomiast przy pracy pompy poza tym zakresem pewien wzrost poziomu drgań jest nieuchronny. Stwierdzenie to znajduje potwierdzenie w literaturze. Jako jego ilustrację na rys. 1 zaczerpniętym z [3, 4] pokazano wzrost poziomu prędkości drgań w miarę oddalania się wydajności od optymalnej.
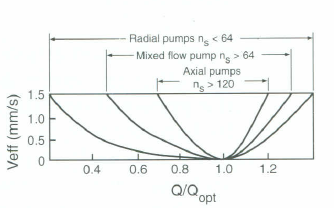
Rys. 1. Wzrost poziomu drgań dla różnych typów pomp przy pracy z wydajnością różniącą się od optymalnej.
Po stronie zdolności konstrukcji pompy do tłumienia drgań producent (projektant) odpowiada za to aby struktura pompy wykazywała sztywność i zdolność do tłumienia drgań odpowiednią do spodziewanych wymuszeń. W szczególności, struktura pompy nie może wykazywać częstotliwości drgań własnych odpowiadających spodziewanym częstotliwościom wymuszeń (a zatem przede wszystkim częstotliwościom obrotowym i łopatkowym), a krytyczne prędkości obrotowe (tj. takie przy których strzałka ugięcia wału na skutek siły odśrodkowej wzrasta) muszą leżeć z dala od prędkości obrotowej. (zazwyczaj powinny się różnić o minimum 20%). Producent pompy nie ma jednak pełnego wpływu na strukturę stanowiska pracy zespołu pompowego, które jest często projektowane przez osobnego projektanta. Znane są sytuacje, gdy układ rurociągów wykazywał częstotliwości drgań własnych zbliżone do częstotliwości obrotowej pompy. Znane są również przypadki generowania drgań przez wymuszenia hydrauliczne generowane na zaworach. Klasyczny sposób zabudowy zespołu pompowego na solidnym, betonowym fundamencie zapewniał z reguły właściwą zdolność do tłumienia drgań. Jednak w przypadku oszczędnościowej zabudowy zespołów pompowych, np., na konstrukcjach stalowych, sztywność takiego podparcia może się okazać niewystarczająca, na skutek czego poziom drgań zespołów pompowych, które na betonowych fundamentach pracowały stabilnie, przy takim sposobie zabudowy nadmiernie wzrasta.
Regulacja parametrów pompy przez zmianę prędkości obrotowej prowadzona w szerokim zakresie stwarza prawdopodobieństwo graniczące z pewnością, że napotkana zostanie któraś z częstotliwości drgań własnych struktury zespołu pompowego co prowadzi do rezonansu.
Wynika z tego, że jeśli producent zespołu pompowego ma brać odpowiedzialność za poziom drgań na stanowisku pracy to powinien mieć co najmniej możliwość zaopiniowania projektu stanowiska aby nie ponosić odpowiedzialności za błędy projektowe skutkujące wzrostem drgań. Próby odbiorcze zgodnie z normą EN-ISO 9906 powinny odbywać się na stanowisku fabrycznym producenta gdyż tam istnieją optymalne warunki do pomiaru parametrów hydraulicznych i energetycznych. Stwierdzenie to nie odnosi się jednak do pomiaru drgań, gdyż fabryczne stanowiska badawcze mają charakter prowizoryczny i często nie cechują się odpowiednią sztywnością podparcia. W [3, 4] podano, że spodziewany poziom drgań na właściwie zaprojektowanym stanowisku pracy jest do 2 mm/s niższy niż na badawczym stanowisku fabrycznym. Z tego wniosek, że jeśli w trakcie badań na stanowisku fabrycznym zostanie potwierdzony wymagany poziom drgań, a na docelowym stanowisku pracy zaobserwowany zostanie wzrost, to należy przypuszczać, że docelowe stanowisko pracy jest wadliwie zaprojektowane.
4. Normy dotyczące poziomu drgań
W obecnym systemie prawnym stosowanie norm nie jest obowiązkowe. Ponieważ jednak są to dokumenty oparte o dobrą praktykę techniczną wskazane jest posługiwanie się nimi celem uzgodnienia wymagań pomiędzy producentem a użytkownikiem.
Dane dotyczące dopuszczalnego poziomu drgań można znaleźć w kilku normach. Zawierająca ogólne wymagania techniczne norma [5] PN-EN ISO 5199 dzieli pompy na maszyny o sztywnym i podatnym podparciu oraz podaje dopuszczalne poziomy drgań dla wzniosu osi pompy h poniżej i powyżej 225 mm. Pompa jest uważana za pompę o sztywnym podparciu jeśli najmniejsza częstotliwość drgań własnych jest co najmniej 25% wyższa od częstotliwości wirowania.
Zdaniem autora podejście takie budzi wątpliwości gdyż sankcjonuje wzrost poziomu drgań dla tzw. pomp o podatnym podparciu, czyli takich, dla których prędkości krytyczne są bliskie obrotowym, co nie jest bezpieczną praktyką konstrukcyjną. Ponadto uzależnienie dopuszczalnego poziomu drgań jedynie od wysokości osi, bez uwzględniania innych czynników wydaje się zbyt daleko idącym uproszczeniem.
Z powyższych względów zaleca się raczej stosowanie niżej omówionych norm.
Norma [7] API 610 stosowana jest powszechnie w przemyśle petrochemicznym. Zdaniem autora, ze względu na to, że opracowana jest na wysokim poziomie technicznym, zasługuje na branie pod uwagę również w innych branżach. Norma ta dla pomp poziomych o prędkości obrotowej do 3600 obr/min i mocy do 300 kW ustala dopuszczalny poziom drgań 3.0 mm/s. Dla wyższych prędkości obrotowych oraz mocy na stopień dopuszcza wzrost poziomu drgań (zgodnie z wykresem zależności od mocy i prędkości obrotowej) jednak nie więcej niż do 4.5 mm/s. Dla pomp pionowych limit ustalono na 5.0 mm/s. Co istotne norma API 610 stwierdza, że podane wyżej limity powinny być dotrzymane w obszarze optymalnej pracy pompy (tj. w pobliżu wydajności nominalnej), a w pozostałej części dopuszczalnego obszaru pracy może nastąpić wzrost drgań o 30%.
Standardem poświęconym w całości kwestii drgań jest norma [5] PN-ISO 10816. Powinna ona być traktowana jako podstawowe źródło wytycznych dotyczących poziomu drgań. Należy zwrócić uwagę, że norma ta składa się z siedmiu części, a dla kryteriów badań odbiorczych najistotniejsza jest część PN-ISO 10816-1 zawierająca wytyczne ogólne oraz część PN-ISO 10816-7, zawierająca specjalne kryteria dla pomp, które są mniej ostre niż kryteria ogólne w części 1 obowiązujące dla innych maszyn wirujących. Należy przypuszczać, że ustalenie mniej rygorystycznych kryteriów dla pomp w intencji autorów normy uwzględnia fakt, że pompy cechują się nieuchronnie występowaniem wspomnianych wyżej wymuszeń hydraulicznych, które w innych maszynach nie mają miejsca.
W części 7 normy ISO 10816 pompy podzielone są na dwie kategorie:
Kategoria I – pompy, dla których wymagany jest wysoki poziom niezawodności i bezpieczeństwa (np. pompy do niebezpiecznych mediów, do krytycznych zastosowań itp.)
Kategoria II – pompy do zastosowań ogólnych i mniej krytycznych
Dla powyższych kategorii norma przewiduje odrębne limity drgań. Ponadto, limity określone dla każdej z kategorii podzielone są na cztery strefy:
Strefa A – drgania dla pomp bezpośrednio po przekazaniu do eksploatacji
Strefa B – drgania akceptowalne w długotrwałej eksploatacji bez ograniczeń czasowych
Strefa C – drgania traktowane jako nieakceptowalne w długotrwałej eksploatacji lecz nie wymagające jeszcze wyłączenia pompy. W tej strefie pompy mogą pracować przez pewien czas, lecz wejście w nią wymaga niezwłocznego planowania środków zaradczych (np. remont).
Strefa D – drgania niedopuszczalne grożące awarią pompy. Wejście w tę strefę powinno skutkować wyłączeniem maszyny.
Dla wyżej określonych kategorii i stref norma podaje poniższe limity wartości drgań:
Powyższe limity ustalone są dla pomp z wirnikami o liczbie łopatek od 3 wzwyż, co jest wyrazem faktu, iż dla wirników dwu- lub jednołopatkowych należy się spodziewać (i akceptować) wyższych poziomów drgań.
Norma ISO 10816-7 w rozdziale 3.4 stwierdza ponadto, że limity drgań powinny być dotrzymane w optymalnym zakresie wydajności (ogólnie rzecz biorąc od 70% do 120% wydajności przy której występuje najwyższa sprawność) natomiast poza tym zakresem może nastąpić wzrost poziomu drgań na skutek wzrostu wymuszeń hydraulicznych. Norma zawiera ilustrujący to wykres zgodny z analogicznym wykresem w normie API 610.
5. Realistyczne wymagania
Jak stwierdzono wyżej norma ISO 10816 przewiduje racjonalne i elastyczne podejście pozwalające na uzgodnienie pomiędzy producentem a użytkownikiem właściwych limitów drgań dla poszczególnych przypadków na podstawie inżynierskich przesłanek. Intencją autorów normy jest uwzględnienie faktu, że w pewnych fizycznych uwarunkowaniach istnieją obiektywne, fizyczne powody do wzrostu poziomu drgań. Usiłowanie utrzymania limitów drgań na najniższym poziomie w tych warunkach wymagałoby stosowania nadmiernie ciężkich, przesztywnionych konstrukcji pomp, co nie znajduje uzasadnienia techniczno-ekonomicznego.
W praktyce zdarzają się przypadki, że autorzy specyfikacji wymagań technicznych dla pomp narzucają wymagania dotyczące drgań idące dalej niż norma ISO 10816 wykorzystując nierzadko pozycję zamawiającego dominującą nad oferentem. Chęć uzyskania jak najniższych poziomów drgań przez użytkowników jest zrozumiała, jednak nie może się to odbywać przy braku zrozumienia obiektywnych przesłanek technicznych, które są podstawą inżynierskiego podejścia zawartego w normie ISO 10816.
Typowe przykłady nadmiernego „śrubowania” wymagań zawartych w specyfikacjach przetargowych są następujące:
1. Wymaganie limitów drgań z części 10816-1 dotyczącej innych maszyn wirujących zamiast limitów z części 10816-7 opracowanej specjalnie dla pomp. Nie uwzględnia to faktu występowania w pompach szczególnych rodzajów wymuszeń (np. hydraulicznych) nieobecnych w innych maszynach wirujących na skutek czego drgania pomp cechują się wyższym poziomem.
2. Traktowanie wszystkich pomp jako krytycznych z kategorii I, co również jest niezgodne z filozofią normy, która zakłada racjonalne dostosowanie wymagań do sytuacji.
3. Wymaganie utrzymania drgań w strefie A przez wieloletni okres gwarancji. Strefa A dotyczy pomp bezpośrednio po uruchomieniu znajdujących się w idealnym stanie technicznym. W trakcie eksploatacji stan ten ulega stopniowemu pogorszeniu, np. na skutek zużycia wirników skutkującego pogorszeniem wyważenia zespołu wirującego czy też na skutek powiększania się luzów łożyskowych. Fakty te uwzględniono w normie poprzez przyjęcie, że w eksploatacji powinny się utrzymywać w strefie B. Zamawiający ma zatem prawo wymagać aby w trakcie prób odbiorczych uzyskać limity ze strefy A lecz powinien uwzględnić, że w trakcie eksploatacji drgania mogą się podwyższyć do wartości dopuszczalnych w strefie B.
4. Wymaganie utrzymania limitów drgań w określonej strefie w całym zakresie regulacji parametrów pompy. W niektórych układach pompowych wymagany zakres wydajności wykracza znacznie poza zakres uważany za optymalny (70% do 120% Qn). Zarówno norma ISO 10816, jak i API 610 na podstawie racjonalnych, inżynierskich przesłanek stwierdzają, że poza tym zakresem należy akceptować wzrost poziomu drgań, w API 610 określony na poziomie 30% wartości zalecanych w optymalnym zakresie wydajności. Oczekiwanie, że pompa pracująca, dla przykładu, z wydajnością 25% nominalnej nie wykaże wzrostu poziomu drgań jest zatem nieracjonalne pod względem technicznym.
5. Wymaganie od dostawcy zespołu pompowego wzięcia odpowiedzialności za poziom drgań na stanowisku pracy, na zaprojektowanie którego dostawca nie miał wpływu.
Na dłuższą metę stawianie wygórowanych wymogów jak wyżej, niezgodnych z racjonalnymi założeniami normy ISO 10816, może zmusić producentów pomp do projektowania konstrukcji nadmiernie przesztywnionych, ciężkich i kosztownych, co nie byłoby ekonomicznie uzasadnione.
6. Podsumowanie i wnioski
- Określanie wymagań dotyczących poziomu drgań zespołów pompowych w specyfikacjach wymagań technicznych stanowiących podstawę zakupu jest zalecaną praktyką, prowadzącą do zakupu pomp o odpowiedniej jakości i trwałości.
- Jako właściwe standardy określające sposób pomiaru i kryteria odbioru zaleca się normy ISO 10816 i API 610.
- Optymalną praktyką jest stosowanie elastycznego podejścia z normy ISO 10816, pozwalającego na racjonalne dostosowanie wymagań do sytuacji. Przykłady narzucania zaostrzonych wymagań , jak te omówione pod koniec p. 5, nie są zgodne z właściwą praktyką inżynierską zawartą w normie.
- Jeśli od dostawcy zespołu pompowego wymaga się zagwarantowania określonego poziomu drgań na stanowisku pracy, to powinien on mieć prawo do co najmniej zaopiniowania projektu tego stanowiska celem wskazania ewentualnych błędów projektowych.
- Jeśli pomiary odbiorcze odbywają się na fabrycznym stanowisku badawczym to stwierdzone tam poziomy drgań mogą wyższe niż na docelowym stanowisku pracy, ze względu na prowizoryczny charakter i mniejszą sztywność zabudowy na stanowisku badawczym. Ewentualne przekroczenie dopuszczalnego poziomu drgań na stanowisku fabrycznym (w zakresie o nie więcej niż 2 mm/s) nie powinno być zatem podstawą do odrzucenia pomp gdyż należy się spodziewać spadku poziomu drgań na właściwie zaprojektowanym docelowym stanowisku pracy i tam powinna nastąpić ostateczna weryfikacja. Natomiast jeśli na stanowisku docelowym stwierdzony zostanie wzrost poziomu drgań w stosunku do stanowiska fabrycznego, to zachodzi domniemanie, że stanowisko to jest błędnie zaprojektowane.
Dr inż. Grzegorz Pakuła
Literatura:
- Gryboś R., Drgania maszyn, Wydawnictwa Politechniki Śląskiej, Gliwice, 2009
- Morel J., Drgania maszyn i diagnostyka ich stanu technicznego, Wydanie polskie : Polskie Towarzystwo Diagnostyki Technicznej, wydanie francuskie: Directions des estudes et recherches d’electricite de France, 1992
- Operating rotodynamic pumps away from design conditions, Eurpopump , Elsevier Science Ltd, 2000
- European Association of Pump Manufacturers , Guide to forecasting the vibrations of centrifugal pumps, Europump publications, 1992
Normy:
- PN-ISO 10816, części 1-7. Ocena drgań maszyn na podstawie pomiarów na częściach niewirujących,
- PN-EN ISO 5199, Wymagania techniczne dla pomp odśrodkowych, Klasa II
- API 610 Pompy odśrodkowe dla przemysłu naftowego, petrochemicznego i gazowego, edycja 11