Ograniczenie kosztów odwadniania kopalń.
1. Wprowadzenie
Podstawową funkcją systemu odwadniania kopalni jest zapewnienie jej bezpiecznej pracy poprzez eliminację zagrożeń wodnych. Osiągnięcie tego celu wymaga ponoszenia kosztów mających znaczenie dla rentowności zakładu górniczego. Koszty te powinny podlegać kontroli i optymalizacji aby w jak najmniejszym stopniu odbiegały od nieuniknionego minimum wynikającego z praw fizyki.
2. Struktura kosztów odwadniania
W celu optymalizacji kosztów odwadniania wskazane jest oszacowanie w jakiej proporcji pozostają do siebie ich poszczególne składniki. Zasadnicze składniki kosztów odwadniania oszacujemy poniżej na przykładzie pompy głównego odwadniania o typowych parametrach : wydajność Q = 500 m3/h, wysokość podnoszenia H = 800 m.
Poniższe oszacowania nie odnoszą się do żadnego konkretnego typu pompy i mają na celu jedynie ustalenie rzędu wielkości poszczególnych elementów. Na koszty odwadniania składają się:
a) Koszty inwestycyjne, czyli koszty zakupu i instalacji zespołu pompowego. Dla pompy o podanych wyżej parametrach koszty te są na poziomie 600 tys. zł. (dokładna wartość zależy od wykonania materiałowego, producenta itp.). Jeśli przyjąć, że taki zespół pompowy amortyzuje się w okresie 10 lat, to w rocznych kosztach odwadniania koszt inwestycyjny pojawi się w postaci amortyzacji na poziomie 60 tys. zł. W praktyce pompy głównego odwadniania znajdują się w eksploatacji dłużej niż 10 lat, co powoduje, że znaczenie kosztu inwestycyjnego ma jeszcze mniejsze znaczenie.
b) Koszty energii elektrycznej do napędu pompy. Pompa o podanych w niniejszym przykładzie parametrach pobiera moc rzędu 1.5 MW. Typowa pompa głównego odwadniania pracuje ok 10 godzin na dobę czyli 3650 godzin w roku. Daje to roczne zużycie energii rzędu 5475 MWh. Przyjmując cenę energii elektrycznej 300 zł/MWh uzyskujemy koszt rocznego zużycia energii przez pompę na poziomie 1. 6425 mln zł.
c) Koszt remontów. Zakres i częstotliwość remontów zależy od jakości wody kopalnianej oraz od konstrukcji i poziomu wykonania pompy. Na podstawie doświadczenia można przyjąć, że średnio pompa wymaga remontu kapitalnego co około 10 000 godzin pracy, a zatem w przybliżeniu raz na trzy lata. Koszt takiego remontu można szacować na ok. 150 tys. zł, a zatem roczny udział kosztów remontu w kosztach odwadniania wynosi ok 50 tys. zł.
d) Koszty obsługi. Współczesne pompy mogą pracować bez obsługi, w trybie automatycznym wymagając co najwyżej okresowej inspekcji. Koszt obsługi wynika zatem w większym stopniu z przepisów i polityki danego zakładu górniczego w zakresie bezpieczeństwa i nadzoru nad układem głównego odwadniania niż z racji technicznych. Przyjmijmy z nadmiarem, że roczny koszt obsługi pompy odpowiada kosztowi jednego etatu, a zatem jest na poziomie 50 tys. zł.
Z powyższego oszacowania wynikają następujące wnioski:
- W całkowitym koszcie odwadniania przy zastosowaniu typowej pompy głównego odwadniania (ok. 1.8 mln zł), dominuje koszt energii (1.64 mln zł) stanowiący ponad 90 % całkowitych kosztów. Ograniczanie kosztów odwadniania musi się zatem koncentrować na ograniczeniu energochłonności.
- Koszt zużywanej energii w silnym stopniu zależy od sprawności energetycznej pomp. Sprawność ta z kolei zależy od jakości konstrukcji i wykonania pompy. W trudnych warunkach kopalnianych początkowa sprawność zespołu pompowego dostarczonego przez producenta ulega zmianie, a zatem koszt zużywanej energii zależy na dłuższą metę od stosowanej polityki remontowej, która decyduje o średniej sprawności pomp w okresie eksploatacji.
Proporcje pomiędzy poszczególnymi składnikami kosztów odwadniania pokazane są na rys.1.
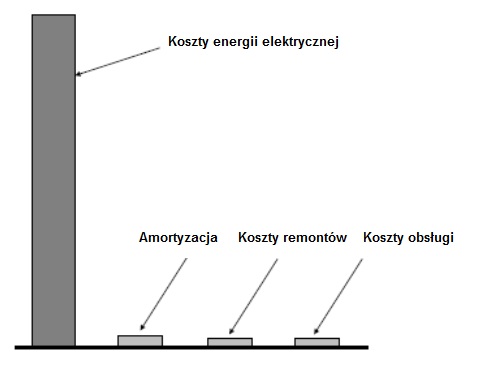
Rys. 1. Proporcje pomiędzy poszczególnymi składnikami kosztów odwadniania
3. Wpływ polityki remontowej na koszt głównego odwadniania.
Pozostając przy powyższym przykładzie pompy głównego odwadniania przeanalizujemy zależność dominującego w kosztach odwadniania kosztu energii do napędu pompy od polityki remontowej.
Moc pobieraną przez pompę można obliczyć ze wzoru:
N = = γ Q H/ ηz ,
gdzie ηz oznacza sprawność zespołu pompowego będącą iloczynem sprawności pompy i silnika.
Rozpatrujemy pompę głównego odwadniania o wydajności 500 m3/h i wysokości podnoszenia 800 m pompującą wodę o gęstości 1000 kg/m3. Dla powyższych parametrów powinno się uzyskiwać sprawność zespołu pompowego na poziomie co najmniej 75%, przy której pobór mocy wyniesie 1453 kW. Gdyby jednak sprawność zespołu o takich parametrach wynosiła 70% to pobór mocy wzrasta do 1557 kW, a dla sprawności 65% do 1676 kW. Jak widać, przy powyższych parametrach taki spadek sprawności oznacza wzrost poboru mocy rzędu 200 kW. Jeśli pompa pracuje 10 godzin na dobę, czyli 3650 godzin w roku odpowiada to zwiększeniu zużycia energii o rząd 730 000 kWh. Jeśli przyjąć cenę kilowatogodziny na poziomie 0.3 złotego to koszt dodatkowej energii wyniesie 219 tys. zł. rocznie. Różnica w rocznym koszcie energii wynikająca z różnic w jakości przeprowadzonego remontu jest zatem na poziomie ceny remontu, a zdecydowanie przewyższa różnice w cenach remontu oferowane przez poszczególnych wykonawców. Z porównania powyższych liczb wynika wniosek, że wybieranie wykonawców remontów pomp jedynie na podstawie ceny remontu bez zwracania uwagi na jego efekt w postaci sprawności jest ekonomicznie nieuzasadnione, gdyż nieznaczne oszczędności uzyskane na cenie remontu mogą być daleko niższe od strat na dodatkowym zużyciu energii. Prawidłowe podejście polega zatem na porównywaniu cen przy wyspecyfikowanej, żądanej od wykonawcy jakości remontu wyrażającej się uzyskaną po remoncie sprawnością energetyczną. Warunkiem wyegzekwowania takich wymagań jest przeprowadzenie po remoncie pomiarów parametrów pompy potwierdzających uzyskanie wymaganej sprawności. Należy zaznaczyć, że sama sprawność pompy pod względem mechanicznym (spokojna praca, dobry wybieg, właściwy poziom drgań itp.) nie jest właściwym miernikiem jakości remontu. Kryterium odbioru pompy po remoncie powinna być zatem, obok wymaganych parametrów podstawowych (wydajność, wysokość podnoszenia) także zmierzona sprawność energetyczna. Formułując wymaganie w tym zakresie należy jednak zachować realizm, gdyż uzyskanie w przypadku pompy mocno wyeksploatowanej sprawności po remoncie odpowiadającej sprawności pompy nowej nie zawsze jest możliwe. Tym niemniej, dopuszczalne pogorszenie sprawności pompy po remoncie w stosunku do sprawności pompy fabrycznie nowej nie może być zbyt znaczne (akceptowalna wartości obniżki sprawności nie powinna przekraczać kilku procent, a najczęściej nie powinna przekraczać 2-3%) gdyż w innym razie, ze względu na znaczny przyrost kosztu zużywanej energii, sens ekonomiczny remontu staje pod znakiem zapytania i realną opcją staje się zakup pompy nowej.
Kolejnym wnioskiem wynikającym z porównania cen remontów oraz cen energii do napędu pompy jest to, że istnieje pewna optymalna częstotliwość dokonywania remontów kapitalnych. W okresie pomiędzy kolejnymi remontami kapitalnymi sprawność pompy na skutek zużycia stopniowo spada. Jeśli z remontem zwleka się do chwili wystąpienia awarii, lub do czasu gdy pompa nie jest już w stanie dać wymaganej wydajności, to w efekcie średnia sprawność w okresie eksploatacji się obniża, a średni koszt wypompowania metra sześciennego wody wzrasta. Zwiększenie częstotliwości remontów odtwarzających sprawność pompy powoduje wzrost remontowego składnika kosztów odwadniania, lecz powoduje obniżenie kosztów energii. Monitorując i analizując na bieżąco oba te składniki kosztu eksploatacji można ustalić optymalną częstotliwość remontów pozwalająca na utrzymanie niżej omawianego wskaźnika kosztów odwadniania na minimalnym poziomie.
4. Wskaźnik energochłonności odwadniania
Z punktu widzenia efektywności energetycznej istotny jest nie tyle chwilowy pobór mocy, co ilość energii zużytej na wypompowanie 1 m3. Dzieląc pobór mocy wyrażony w kW przez wydajność wyrażoną w m3/h otrzymujemy wskaźnik pokazujący ile kilowatogodzin potrzeba do wypompowania jednego metra sześciennego wody w konkretnym układzie pompowym. Pobór mocy jest proporcjonalny do parametrów, wydajności Q i wysokości podnoszenia H. Istnieje pewna minimalna wartość energii, jaką należy zużyć na pompowanie cieczy na wysokość H, poniżej której nie można zejść.
To minimalne zużycie energii na wypompowanie metra sześciennego wynosi:
Nmin /Q = γ Hg,
gdzie Hg jest wysokością geometryczną, na jaką pompuje się wodę.
Tak określony współczynnik energochłonności nie może służyć do porównywania różnych układów odwadniania, gdyż zależy on od geometrycznej wysokości podnoszenia, która różni się dla poszczególnych układów. Wskaźnik ten pozwala jednak ocenić efektywność energetyczną danego układu odwadniania poprzez porównanie rzeczywistego zużycia energii na wypompowanie metra sześciennego ze zużyciem minimalnym.
Zejście poniżej takiego minimalnego jednostkowego zużycia energii jest fizycznie niemożliwe. W trakcie eksploatacji należy natomiast dążyć do tego aby rzeczywiste jednostkowe zużycie energii przewyższało powyższe minimum w możliwie najmniejszym stopniu.
Jak wynika z dwu powyższych wzorów zwiększenie rzeczywistego zużycia energii ponad fizyczne minimum wynika zasadniczo z dwu przyczyn:
a) Z faktu, że rzeczywista sprawność zespołu pompowego ηz jest mniejsza od jedności. Na wartość sprawności energetycznej zespołu pompowego wpływa głównie polityka remontowa, o której mowa w punkcie poprzednim oraz dobór pompy do układu, o czym mowa w punkcie kolejnym.
b) Z tego, że całkowita wysokość podnoszenia H w układzie pompowym jest większą od wysokości geometrycznej o wielkość strat w rurociągach.
O ile wysokość geometryczna jest wartością stałą to na wysokość strat można do pewnego stopnia wpływać. Układ głównego odwadniania zazwyczaj składa się z kilku rurociągów, często o różnych średnicach. W celu ograniczenia strat wskazane jest pompowanie przez wszystkie dostępne rurociągi jednocześnie gdyż wtedy prędkości przepływu, a tym samym straty ulegają zmniejszeniu w porównaniu z pompowaniem przez pojedynczy rurociąg. Z tego samego powodu korzystne pod względem energetycznym jest pompowanie jak najmniejszą liczbą pomp jednocześnie. W układzie odwadniania należy eliminować źródła dodatkowych strat, np. w postaci odcinków rurociągów o mniejszej średnicy, armatury o zbyt wysokich współczynnikach oporu itp. Dla przykładu: w rurociągu o średnicy 400 mm, przy przepływie 1000 m3/h wysokość strat wynosi około 1.2 m na 100 m długości rurociągu. Przy tej samej wydajności w rurociągu o średnicy 300 mm straty wzrastają do około 5.2 m na 100 m długości. Eliminacja tego rodzaju strat wymaga pewnych nakładów inwestycyjnych. Pewne oszczędności energii można też uzyskać bezinwestycyjnie dbając o właściwą jakość eksploatacji układu, np. o to aby wszelka armatura odcinająca na trasie rurociągu była w pełni otwarta podczas pompowania, aby kosz ssawny nie był zanieczyszczony itp. Jeśli nie zagraża to bezpieczeństwu pompowni na skutek zmniejszenia retencji wskazane jest unikanie pompowania przy niskim poziomie cieczy w zbiorniku ssawnym tzn. wyłączanie pomp do czasu gdy woda napłynie do wyższego poziomu w zbiorniku.
Podkreślenia wymaga fakt, że działania zmierzające do oszczędzania energii poprzez ograniczenie oporów przepływu dają najlepszy efekt dopiero wtedy gdy idą w parze z dostosowaniem parametrów pomp. Jeśli bowiem podejmiemy działania w kierunku ograniczenia oporów, np. przez pompowanie przez więcej niż jeden rurociąg lub ograniczenie oporów na armaturze, to może się okazać, że na skutek zmiany charakterystyki układu punkt pracy pomp przesunie się na wyższe wydajności co ograniczy oszczędności energetyczne na skutek pracy pomp poza optymalnym zakresem sprawności. Jeśli zatem uzyskane zostaną znaczące redukcje oporów przepływu to dla ich pełnego wykorzystania powinna temu towarzyszyć odpowiednia redukcja parametrów pompy.
5. Wpływ doboru pompy do układu na sprawność.
Podkreślić należy, że na wartość zużycia energii najważniejszy wpływ ma nie maksymalna (katalogowa) wartość sprawności, lecz sprawność w rzeczywistym punkcie pracy. Jak wiadomo punkt pracy pompy przypada przy takiej wydajności, przy której charakterystyka pompy przecina się z charakterystyką układu. W celu poprawnego doboru pompy należy zatem oszacować charakterystykę układu, a zatem ustalić jak straty zmieniają się z wydajnością. Powszechna praktyka polegająca na doborze pompy z wirnikami o maksymalnej średnicy, z najbliższą liczbą stopni przy której wysokość podnoszenia przekracza wymaganą, w niektórych przypadkach prowadzi do zainstalowania pompy z wysokością podnoszenia z kilkudziesięciometrowym nadmiarem, co powoduje, że pompa pracuje w układzie ze zbyt wysoką wydajnością. Jest to niekorzystne pod względem energetycznym z dwu powodów: po pierwsze, dla zwiększonej wydajności sprawność pompy jest obniżona w stosunku do maksymalnej, a po drugie zwiększona wydajność powoduje zwiększenie oporów przepływu. Nadmierne zwiększenie wydajności prowadzi w skrajnych przypadkach do przeciążenia silnika i do pracy w kawitacji. Przymknięcie zaworu tłocznego powoduje uniknięcie tych zjawisk , ale oznacza pracę pompy przy zwiększonym jednostkowym zużyciu energii ze względu na konieczność pokonywania dodatkowych strat na zaworze. Należy mieć świadomość, że przymknięcie zaworu tłocznego powoduje spadek bezwzględnego poboru mocy, ale najczęściej oznacza wzrost poboru jednostkowego odniesionego do wypompowanego metra sześciennego. Praktyka eksploatacyjna polega często na tym, że pompowanie prowadzone jest przy w pełni otwartych zaworach tłocznych dopóki nie występują problemy z przeciążeniem silnika lub kawitacją, a jeśli problemy te się pojawiają, to są eliminowane przez przydławienie pompy. Taki sposób prowadzenia eksploatacji zapewnia uniknięcie podstawowych problemów ruchowych lecz nie daje gwarancji, że pompowanie prowadzone jest w optymalny sposób z punktu widzenia energetycznego. W wielu przypadkach optymalny wskaźnik zużycia energii na wypompowanie metra sześciennego można uzyskać przez ograniczenie parametrów pompy drogą zmniejszenia średnicy wirników. Takie rozwiązanie pozwala uniknąć dławienia zaworem.
W celu określenia najlepszego pod względem energetycznym doboru pompy do układu potrzebne jest przeprowadzenie analizy charakterystyk pompy i układu. W zasadzie tego typu analizy powinny być przeprowadzone na etapie prac projektowych mających na celu dobranie pompy do układu. W praktyce wskazane jest przeprowadzenie takiej analizy już w trakcie eksploatacji, a to z tego względu, że rzeczywiste charakterystyki konkretnego egzemplarza pompy oraz rzeczywista charakterystyka układu, często różnią się od charakterystyk teoretycznych analizowanych na etapie projektowania. Z tego względu w trakcie eksploatacji celowe jest przeprowadzenie weryfikacji doboru pompy do układu, mającej na celu zapewnienie, że pompa pracuje w obszarze swojej najwyższej sprawności.
Pompy głównego odwadniania posiadają dużą wysokość podnoszenia ze stopnia i wobec tego nie pokrywają gęsto całego zakresu możliwych wysokości podnoszenia. Może się zdarzyć, że pompa o pewnej liczbie stopni nie zapewnia wymaganej wysokości podnoszenia, a pompa o liczbie stopni o jeden większej posiada nadmiar parametrów. Taki przypadek pokazano na rys. 2. Jest to przypadek przykładowy. Charakterystyki pompy i rurociągu nie odnoszą się do żadnego konkretnego typu pompy ani do konkretnego układu lecz zostały narysowane poglądowo. W przypadku tym należy dobrać pompę o wydajności 500 m3/h do układu pompowego, którego charakterystyka pokazana jest na rys. 2 linią kropkową.
Charakterystyka ta odpowiada charakterystyce układu pompowego o wysokości geometrycznej 710 m z rurociągiem o średnicy 300 mm i o długości 800 m. Dla wydajności 500 m3/h wysokość strat wynosi około 10 m, czyli pompa przy tej wydajności powinna być dobierana na wysokość podnoszenia 720 m. Analizujemy dobór do tego układu pompy o wydajności nominalnej 500 m3/h (czyli właściwej dla wymaganej wydajności) i wysokości ze stopnia 70 m. Charakterystyki H(Q) dla tej pompy pokazane są na rys. 2 linią ciągłą, a charakterystyka sprawności η(Q) linią przerywaną. Pompa 10-cio stopniowa przy nominalnej wydajności posiada wysokość podnoszenia 700 m, a zatem do wymaganych 720 m brakuje jej 20 m. Na skutek tego charakterystyka pompy 10-cio stopniowej przecina się z charakterystyką układu pompowego przy wydajności ok. 430 m3/h i przy wysokości podnoszenia ok. 718 m. Pompa ta zatem nie spełnia wymagań. Nie tylko nie daje wymaganej wydajności, lecz ponadto jej punkt pracy wypada poza zakresem optymalnych sprawności. Jak widać z rys. 2, pompa, której najwyższa sprawność wynosi ok. 79%, w tym układzie, na skutek nieprawidłowego doboru („zadławienia” przez nadmierną wysokość podnoszenia) pracowałaby ze sprawnością ok. 74 %. Pobór mocy (który można obliczyć na podstawie Q, H i sprawności lub odczytać z niepokazanej na rysunku charakterystyki N(Q) ) wyniósłby w tym przypadku ok. 1137 kW, zakładając że pompowana jest czysta woda o typowym ciężarze właściwym.
Z punktu widzenia efektywności energetycznej istotny jest nie tyle chwilowy pobór mocy, co ilość energii zużytej na wypompowanie 1 m3. Dzieląc pobór mocy wyrażony w kW przez wydajność wyrażoną w m3/h otrzymujemy wskaźnik pokazujący ile kilowatogodzin potrzeba do wypompowania jednego metra sześciennego wody w konkretnym układzie pompowym. W powyższym przypadku dla pompy 10-cio stopniowej uzyskujemy wskaźnik 2.64 kWh/ m3. Należy zwrócić uwagę, że korzystnie na wartość tego wskaźnika w tym wypadku wpływa fakt, że przy zmniejszonej wydajności występuje zmniejszona wysokość podnoszenia na skutek mniejszych strat przepływu w rurociągu, natomiast niekorzystny wpływ wywiera obniżenie sprawności na skutek pracy pompy poza optymalnym zakresem.
Z kolei gdyby zastosować pompę jedenastostopniową (cechującą się nadmiarem wysokości podnoszenia ponad wymagania tego układu) to jej punkt pracy, wynikający z przecięcia charakterystyki pompy z charakterystyką rurociągu wypadłby przy wydajności ok. 645 m3/h i przy wysokości podnoszenia ok. 728 m. Pompa nie powinna pracować w takim punkcie. Po pierwsze, znajdowałaby się poza obszarem optymalnych sprawności, gdyż sprawność w tak ustalonym punkcie pracy wynosi zaledwie 71%. Ponadto, jak wynika z charakterystyki, wymagane NPSHr w tym punkcie wzrasta do ok. 7 m, co w znacznym stopniu ogranicza zdolności ssawne pompy i grozi wystąpieniem kawitacji przy nieznacznym obniżeniu poziomu wody w zbiorniku ssawnym. Pobór mocy pompy wyniósłby ok. 1802 kW, a więc więcej niż moc silnika dobranego na parametry nominalne. Decydując się świadomie na taki dobór można by uniknąć przeciążenia instalując silnik o zwiększonej mocy, ale byłoby to niekorzystne od strony energetycznej, gdyż wskaźnik kilowatogodzin na wypompowany metr sześcienny wyniósłby w tym przypadku 2.79 kWh/ m3. Wzrost w stosunku do obliczonej poprzednio wartości wynika z dwu przyczyn: po pierwsze na skutek wzrostu wydajności wysokość strat w rurociągu wzrasta do wartości ok. 18 m, a po drugie, pompa pracuje z jeszcze bardziej obniżoną sprawnością.
Dla poprawy jakości doboru wskazane jest zastosowanie wirników o zredukowanej średnicy. Średnicę tę należy tak dobrać, aby wydajność pompy była zbliżona do wymaganych 500 m3/h.
Celowe jest zastosowanie takiej średnicy, która daje wydajność nieco wyższą, co wynika z dwuch przyczyn.
Po pierwsze, zapewnia to pewien zapas parametrów pompy na zużycie w trakcie eksploatacji, a po drugie ze wzrostem stopnia redukcji średnicy wirników pogłębia się spadek sprawności, więc średnicę należy redukować w możliwie najmniejszym zakresie. Na rys. 2 pokazano linią kreskowo-punktową przykładową charakterystykę pompy 11-sto stopniowej z wirnikami o zredukowanej średnicy, która przecina się z charakterystyką układu przy 520 m3/h i wysokości podnoszenia ok. 721 m. Na skutek redukcji średnicy wirników zmienia się też charakterystyka sprawności η(Q). Jak wiadomo, obniża się sprawność maksymalna, a ponadto jej położenie przesuwa się w kierunku niższych wydajności. Charakterystykę sprawności pompy o zredukowanej średnicy wirników pokazano na rys. 2 linią kreskowo – punktową z podwójnymi punktami. Jak z niej wynika sprawność pompy przy 520 m3/h wyniesie około 76%. Z tego z kolei wynika pobór mocy 1344 kW oraz wskaźnik energochłonności 2.585 kWh/ m3. Jak widać wskaźnik ten jest korzystniejszy niż dla pomp 10 i 11-sto stopniowych z pełnymi średnicami wirników. Stopień redukcji średnicy wirników należy zoptymalizować w taki sposób aby uzyskać możliwie najkorzystniejszy wskaźnik energochłonności. Jak wynika z powyższego nadmierna wartość średnicy prowadzi do obniżenia sprawności na skutek pracy ze zbyt wysoką wydajnością.
Z drugiej strony, zbyt głęboka redukcja średnicy również powoduje spadek sprawności. Zaleca się zatem przeanalizowanie kilku stopni stoczenia średnicy wirników celem ustalenia wartości zapewniającej optymalny wskaźnik zużycia energii na wypompowanie metra sześciennego. Oprócz tego, jak wspomniano, należy też mieć na uwadze zapas parametrów na zużycie pompy, a także bardzo istotny czynnik jakim jest NPSH przy wydajności w punkcie pracy.
Pokazany wyżej przykład doboru pompy ilustruje stwierdzenie, że dobieranie pompy na określony, pojedynczy punkt Q, H nie jest prawidłową praktyką, gdyż nie umożliwia pełnej analizy skutków wynikających z niedopasowania parametrów pompy do układu. Dopiero analiza prowadzona na charakterystyce układu pompowego pozwala na przewidzenie wynikowego punktu pracy ze wszystkimi konsekwencjami w postaci sprawności, poboru mocy i zdolności ssania. Jak wspomniano przykład ten nie dotyczy żadnego konkretnego przypadku lecz w sposób jakościowy ilustruje wpływ doboru pompy na uzyskiwaną sprawność.
6. Wpływ sposobu eksploatacji na sprawność.
Jak wspomniano wyżej utrzymanie wysokiej, średniej sprawności w okresie eksploatacji zależy od polityki remontowej. Jednak na sprawność pompy pewien wpływ ma też sposób jej eksploatacji pomiędzy remontami. Oprócz tak oczywistych spraw jak unikanie zbyt wysokich oporów mechanicznych na skutek braku czynnika smarującego w łożyskach lub zbyt silnego dokręcenia dławnic, istotne znaczenie ma też obsługa tarczy odciążającej.
Sprawność pompy zależy w silnym stopniu od względnego położenia wirników i kierownic. Położenie to w pompie z tarczą odciążającą zależy od stopnia jej zużycia. Jeśli zespół wirujący na skutek zużycia tarczy odciążającej przesuwa się na tyle, że strugi wypływające z wirników trafiają nie w kanały kierownic lecz w ich ścianki sprawność ulega silnemu pogorszeniu. Sprawność pompy jest najwyższa gdy osie kanałów wirników i kierownic pokrywają się. Niesymetryczne ustawienie kanałów wirników i kierownic względem siebie powoduje obniżenie sprawności nawet w przypadku gdy nie następuje jeszcze uderzanie strugi w ściankę. Dlatego, w celu utrzymania wysokiej sprawności eksploatacyjnej obsługa powinna monitorować położenie wskaźnika przesuwu wału i dążyć do tego aby zespół wirujący znajdował się w optymalnym położeniu. Można to osiągnąć przez okresową wymianę pierścieni tarczy odciążającej i/lub podkładek regulacyjnych przed tarczą.
PODSUMOWANIE I WNIOSKI
Zasadniczym składnikiem kosztu głównego odwadniania jest koszt energii elektrycznej mogący przekraczać 90% całości kosztów.
W celu jego redukcji konieczne jest prowadzenie właściwej polityki remontowej polegającej na:
a) prowadzeniu remontów kapitalnych z optymalną częstotliwością zapewniającą utrzymanie wysokiej średniej sprawności w okresie eksploatacji,
b) wymaganie od wykonawców remontów kapitalnych pomp uzyskania gwarantowanej wysokiej sprawności energetycznej i sprawdzanie tego warunku na stacji prób w charakterze kryterium odbioru remontu.
Duże znaczenie ma również prawidłowy dobór pomp do danego układu pompowego, który powinien być przeprowadzany indywidualnie dla każdego przypadku.
Należy również prowadzić eksploatację pompy we właściwy sposób pozwalający na utrzymanie wysokiej sprawności energetycznej.
W celu optymalizacji kosztu pompowania wskazane jest rejestrowanie ilości wypompowanej wody oraz ilości energii elektrycznej zużytej w tym celu oraz monitorowanie i analizowanie obliczonego na tej podstawie wskaźnika energochłonności.
Dr inż. Grzegorz Pakuła